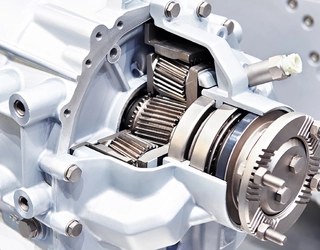
Phosphating coatings
contact us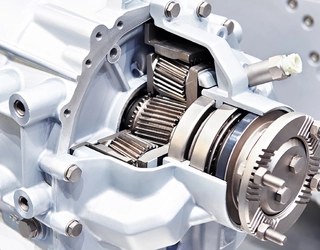
A major trend in automotive fastening technology is smaller parts using high strength steel fasteners to reduce component weight. The expanding new categories of fasteners replace traditional permanent joining methods, such as adhesives, rivets, and welding, which inherently do not allow component disassembly. Additionally new powertrain, gearbox, and fastener designs are being investigated for use in electrical vehicles.
In these applications KeyKote phosphate solutions provide corrosion and wear resistance. These coatings readily absorb oil and other lubricants, providing predictable coefficient of friction properties. Read more about the phosphate coatings in our article published in Fastener and Fixing magazine.
Automotive engineers can choose between 3 types of coating:
Our sustainable processes are nickel-free, an important consideration for applicators as it reduces sludge formation to meet local waste water discharge criteria.
To find out more about protecting your high tensile fasteners, contact us today.
*HE also known as hydrogen assisted cracking (HAC) and hydrogen-induced cracking (HIC), describes the embrittling of metal after being exposed to hydrogen.