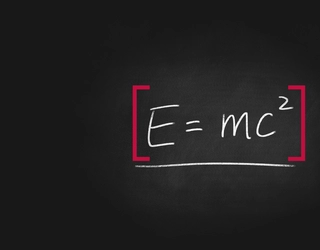
Are environmental and performance standards getting you hot under the hood?
contact us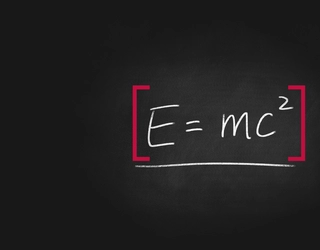
Albert Einstein famously once said that insanity is doing the same thing over and over again and expecting different results. Perhaps insanity is a bit strong, but it is a nice summary of the power of cause and effect. For optimal results, optimal inputs are a must, and it would be unrealistic to expect otherwise. This principle can be applied to many different areas of life, and vehicle components used in ADAS (Advanced Driver Assistance Systems) are no exception.
The transition towards level 3 and 4 vehicle autonomy presents several challenges. As advanced safety systems become increasingly complex, they require greater processing power and suitably tough materials, particularly where the die attach material is concerned.
Increased processing power produces excess heat, which needs to be removed to sustain performance and minimize the risk of failure. From a thermal dissipation point of view, your choice of die attach material can make all the difference, with huge repercussions if it is unable to withstand the demands of operation – that’s a whole lot of responsibility for one material! It is fair to say that the choice of die material for IC Substrate packages used in ADAS, which are essentially the brain of the system, has a major impact on overall vehicle reliability and performance.
Moving away from lead solder
Historically, tin/lead solder was the die attach material of choice for semiconductors. As the required performance level of ADAS has drastically increased, it is clear that the input material also needs to change to withstand harsher operating conditions. To expect better outcomes with the same method and materials would be, according to Einstein’s definition, insanity.
Performance is crucial, but it is not the only factor behind the need to transition towards better die attach materials. Regulatory pressures also play an important part in this journey. The use of lead-containing alloys has been banned in other industries for some time on health and environmental grounds. RoHS, REACH and ELV regulations currently allow the use of lead as a die attach material thanks to an exemption for vehicle manufacturing. With this now set to expire in 2024, however, the reality is that lead is on borrowed time, having been progressively replaced by materials that are better suited for harsh environments and higher thermal and electrical budgets.
Overcoming environmental and regulatory concerns
Most advanced processing packages used in ADAS hardware encounter some degree of thermal dissipation challenges. Their critical role within overall vehicle performance and safety, mean that investment in the right mix of high-quality materials is a necessity. Existing epoxy solutions, like electrically conductive adhesives, which do not contain lead, help to overcome environmental and regulatory concerns. The issue is that these provide insufficient heat dissipation, greatly increasing the risk of performance issues and failure. Materials must therefore be specified with regulatory factors in mind, along with an understanding of the performance requirements of the application, as determined by the OEM. Given that these can vary, a degree of design and flexibility is also necessary from a cost management perspective.
Long term performance and safety benefits
Emerging materials such as Atrox offer a potential solution to the twin challenges of design and performance flexibility. While it offers better thermal conductivity, it also circumvents legislation relating to the use of lead. When compared with traditional materials, the performance and reliability benefits over the long term are significantly greater.
MacDermid Alpha Electronics Solutions has developed the proprietary capability to adjust the level of silver and thermoset resin within Atrox to deliver a range of heat dissipation. By varying the concentration of each constituent, this can alter the thermal and conductive properties of the material solution. This can be tailored to the precise demands of the application, whether for standard ICs, power packages or high-end applications.
The benefit of using materials from the Atrox series is that manufacturers can meet their performance requirements across a thermal conductivity spectrum ranging from 2 to 180W/mK. Additionally, to produce the same number of units compared to lead soldering within a given timeframe, the number of machines required is reduced by 25%.
ADAS have now gone beyond a supporting role within the functioning of a vehicle. As we transition into level 3 and 4 autonomy these are vital in terms of reliability and safety and must therefore be prioritized accordingly. Given their importance, a better class of material must be used as part of the die attaching process within semiconductor production.
As we move away from lead-based soldering solutions, you don’t need to be Albert Einstein to see the long-term performance and safety advantages of Atrox .
Discover with MacDermid Alpha Electronics Solutions how Atrox can help improve ADAS performance and reliability .