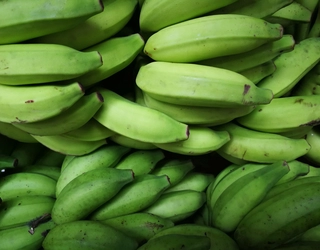
What do green bananas and electric powertrains have in common?
contact us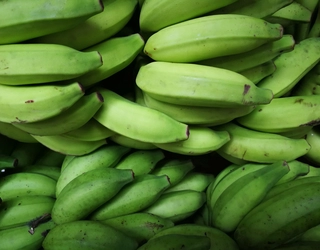
Chris Klok, Director of Vehicle Electrification at MacDermid Alpha Electronics Solutions
For many incumbent OEMs, some EV technology remains an unknown – a green banana, if you like. There is often a perception that some technologies are simply unripe for mass market manufacturing. However, this is rarely the case. What do green bananas and EV technology have in common? There is a perception that both are too new, or not quite ready for consumption.
Proposed new technology is often seen as a risk in the eyes of a vehicle manufacturer. OEMs are known to be risk averse and want proven, established methods of production that won’t let them down. However, through the transition to electric powertrains from internal combustion engines, there are inevitably green bananas – new techniques that aid the production of more reliable, safer vehicles.
The race to electrification has been underway for over a decade. OEMs are faced with the threat of new EV start-ups and the pressures on the automotive industry to deliver electric vehicles has never been greater. What’s more, OEMs need the right mindset in place for this change to happen successfully. Perhaps more crucially, OEMs are often wary of new technologies, because of the proposed risk they represent. Even though many of these technologies new to the automotive industry have been proven in other industries.
The incumbent OEMs are still learning about the 'new' technology in EVs far later in the race to electrification. Today’s electric vehicles aren’t attractive to all motorists because they’re not seen as future-proof, with many believing they cannot be used for long journeys due to shorter ranges. In some cases, that’s true, but many of the EVs with longer ranges come with larger batteries. This is an example of OEMs playing catchup and not necessarily having the best resources to progress their brands into the age of electrification.
Currently Tier 1 and Tier 2 suppliers have more experience and intellectual property (IP) than OEMs which already have dedicated in-house engineering teams to retain control and market differentiation. OEMs are in the process of transitioning from vehicles designed primarily with mechanics to electronics, which raises the question if it’s possible for them to become fully engineering dependent.
One of the biggest challenges for OEMs is making EVs more affordable, while reaching the demands for an acceptable range. For many, the answer has been to add more batteries, but this adds more cost to the consumer and more weight to the vehicle.
What if it was possible to add range without increasing weight? That’s what MacDermid Alpha Electronics Solutions focuses on, through the design of the inverter. When the efficiency of the inverter power conversion is maximized, range is extended without the need for extra batteries. Most current inverter designs use silicon-based power modules with soldered and wire-bonded interconnects.
While seemingly more economically viable than alternative techniques, soldering has relatively low thermal and electrical conductivity, with low melting points, which limits EV operating temperatures. What if it was possible to instead use silicon carbide semiconductors as part of an approach that improves inverter efficiency. Sounds impossible? A little too much like green bananas perhaps?
At MacDermid Alpha Electronics Solutions, we have been helping OEMs meet this challenge for years through silver sintering technology. Far from being a green banana, it’s actually a tried-and-tested process for die-attach and substrate-attach material that delivers several benefits over conventional soldering in selected applications.
In our experience, silver sintering can help overcome the thermal dissipation and high temperature stability challenges associated with traditional power module interconnects. It works by sintering silver particles to form bulk silver bonds through atomic diffusion. This gives a more stable bond with higher stability and lower thermal resistance, enhancing performance at higher operating temperatures, since the melting temperature of silver is 962 °C.
Watch the video below to learn how MacDermid Alpha Electronics Solutions is using silver sintering technology to support electric vehicle reliability.