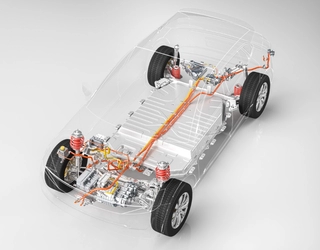
Aluminum coating
contact us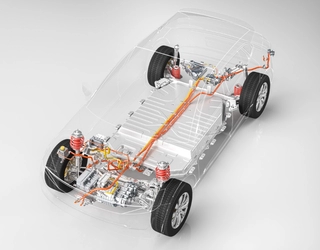
As the electric vehicle (EV) revolution grows, there is increasing demand for aluminum due to its excellent structural strength and low mass density.
Aluminum is strong, corrosion resistant, and sustainable. Recycling is easy; over 75% of the aluminum produced in the last 100 years is still in use.
.In the EV market the prime consumer concern is ‘range anxiety’, and for a given battery capacity, the heavier the vehicle, the shorter the range. Using aluminum can reduce the weight of a component by up to 60% compared to steel.
Aluminium plays a significant role in the light-weighting of electric and hybrid vehicles. As well as being used or structural body components and Body In White (BIW)applications; It is also used for components such as construct battery packs, heat sinks , motor housings and cabin heaters or its good thermal transfer capabilities. Additionally It is increasingly being used in brake calipers, replacing cast iron
Zinc/Tin/Aluminum co-deposited self-piercing rivets are increasingly being used for Aluminum body panel construction as they are lightweight and help to prevent contact corrosion.
Aluminum forms a natural invisible oxide film which provides protection in low service conditions but does not protect against harsh environments such as:
Combined these all need careful consideration so that the aluminum component functions for expected life cycle without prematurely corroding.
We offer 3 types of surface treatment for aluminum, or surfaces which come into contact with the metal.
Zinc-nickel plating is usually applied where specifiers want the highest performance with the lowest deposit thickness. By specifying zinc-nickel, components can resist more than 1000 hours neutral salt spray (ISO 9227 & ASTM B117) with no effect on the dimensional tolerance of threaded components.
Increasing concerns over the health and ecological effects of hexavalent chromium has inspired the development of alternative approaches and technologies for various coating types. Our development of chromate-free Iridite conversion coatings are direct replacements for chromium containing finishes in automotive applications.
Our Oxidite anodizing systems demonstrate our expertise in cleaning, etching, desmutting, coloring and sealing for the anodizing industry. Developed and refined to meet automotives' exacting needs to enhance and protect pure and alloyed aluminum.
Want to know more about protecting aluminum in automotive applications? Contact us today.